Central cartridge exhaust system – 610 series
for the central suction and filtering of dust and smoke!
Application
- for strongest extraction and filtering tasks
- Installation for indoor or outdoor use
- Central extraction of several workstations and welding booths
- Extraction of cutting tables
- Extraction of welding hoods for robots
Technical specifications
- Flow rate: 4,000 – 36.000 m³/h
- Power consumption: 5.5 kW – 37 kW
- useful as combined devices
Scope of delivery
Depending on the application:
- Single complete machine or in combination with f.e. cutting table
- complete with piping, depending on application
- designed according to your individual needs
The central extraction system for grinding, blasting and heaviest plasma cutting applications
This large scale exhaust system splits filter and radial fan in separate units. We recommend this filter system for hardest grinding, welding and cutting applications. It is available up to an exhaust capacity of 36,000 m³/h. Filter systems of the 610 series can be placed inside or outside the workshop. Filter systems for outside placement are equipped with a separate control cabinet, a 90° silencer outlet and special UV resistant coating. For outside placement HERR Industry Systems also offers a special explosion protected version of the system.
Filter systems of the 610 series use a multiple of 20 m² surface HISTec® ePTFE cartridges. The Siemens® logic monitors the work procedure and initiates the cleaning when the filter cartridges are stuffed. Cleaning is executed only when necessary – this saves energy and increases the filter cartridge lifespan. The soft, quiet and efficient cleaning via the HiRoto® rotary nozzles saves air (energy) and stresses the filter cartridge less than conventional cleaning procedures via air pulse. Optionally series 610 filter systems can be equipped with a frequency inverter to adjust the airflow according to the production needs. This saves energy and money.
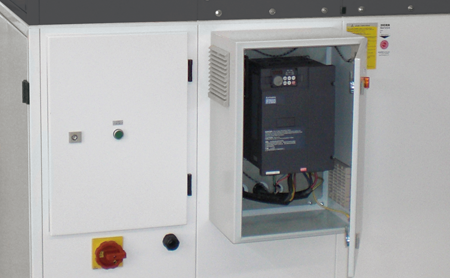
Frequency converter
Frequency converters are used especially in the extraction of several welding workstations. They adjust the airflow to the workload. Through sensors, the filter system recognizes the required air pressure. The frequency converter will adjust the fan speed to the conditions.
This increases the life of the filter cartridges, reduces the need for exhaust air and helps to reduce the power consumption. The additional cost of the frequency converter pays for itself in a short time.
Fire protection
HERR Industry System filter systems are among the safest filtering systems on the market: pre-filter chamber, vertically built filter cartridges, special routing of the air in the filter chamber, complete cleaning of the filter cartridges at the end of the working day and a special design of the cover of the dust box effectively prevent the occurrence of filter fires.
Optional additional options for firefighting are available: sensors for temperature-sparks monitoring, CO2, water foam deletion, automatic partitioning of the filter.
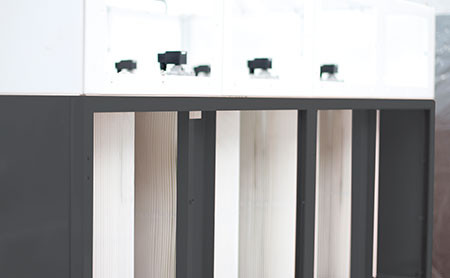
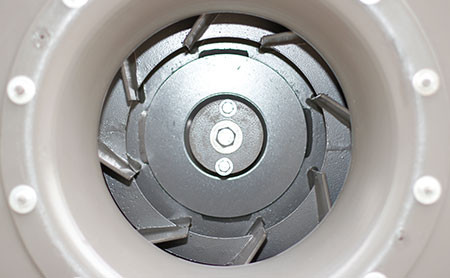
Fan
The selection of a suitable fan not only saves energy, it is also important for the life of the filter cartridges.
With increasing life span of the filter the air resistance of the filter cartridge increases slightly but steadily. The fan must be able to compensate this justice. This is best accomplished with a control via frequency converters.
Convenient and safe dust disposal
The dust is collected in an area under the filter in a dust box. During operation, the container is pneumatically pressed against the filter. To empty it can be released and moved out on rollers.
Cheap PVC waste bags minimize contact to dust and can be easily removed and replaced. The container should be emptied at least once daily. Optionally, a emptying in barrels or with the rack locks are available at extra cost.
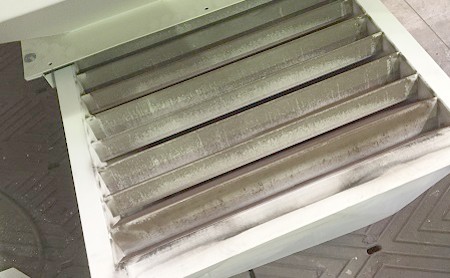
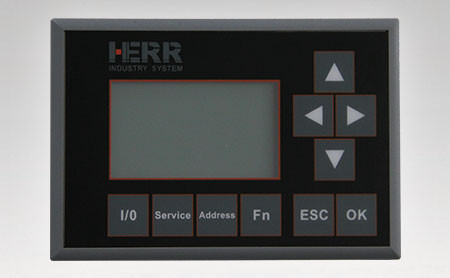
Intelligent control
The central suction systems from HERR Industry System using Siemens control and a specially developed software from HERR Industry System.
All important functions and messages of the control are displayed on a LCD screen. Important areas are protected with a password to prevent accidental deletion or change of parameters. The comfortable control simplifies operation and provides important instructions for maintenance and problem diagnosis.
Certification by IFA
The German Institute for Occupational Safety and Health (IFA) confirmed that the HISTec® ePTFE coated cartridge filter, filter welding and cutting particles of size 0.1 microns.
The filter efficiency is up to 99.9 %.
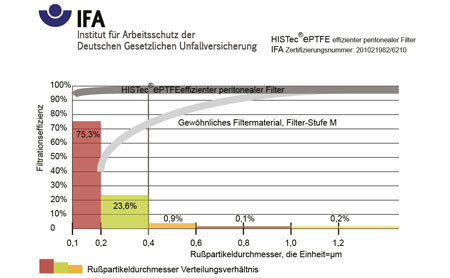
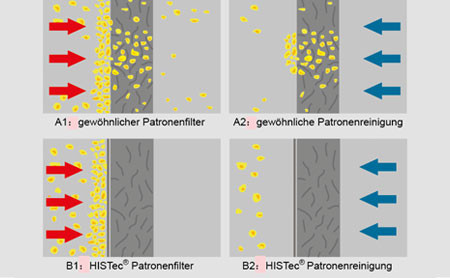
ePTFE coating of the filter cartridges
According to the test data of the German Institute for Occupational Safety and Health IFA the collected dust particles have a diameter between 0.1 – 1.0 μm.
More than 90 % of the dusts having a diameter of less than 0.4 microns. This particles may access the lungs directly through the alveoli, penetrate into the bloodstream and cause several diseases.
Welding and cutting dusts therefore represent a major health risk. With ordinary filter material particles are filtered less than 0.4 microns inadequately. More than 90 % of the particles can exert their harmful effects despite filtration. HISTec® ePTFE cartridge filter will help to prevent your workers effectively!
HISTec® filter cartridge
The filter material of the ePTFE coated HERR filter cartridge is folded like the bellows of an accordion. The distance between the folds is consistent and is fixed by gluing of the filter in the bottom and lid. The folding angle of filter cartridge is less than 2°, thus provids an optimum of filter surface with high efficiency airflow.
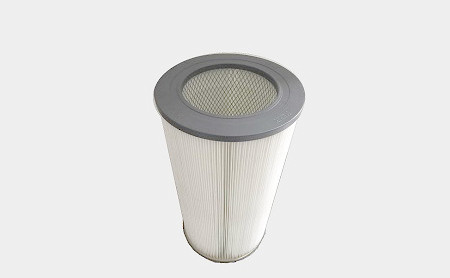
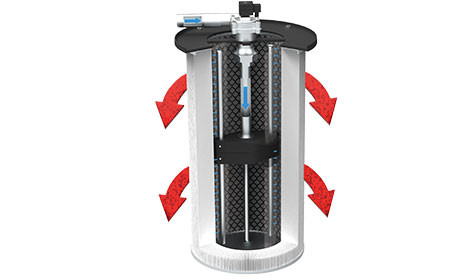
Automatic filter cleaning by HiRoto® H-nozzle
The rotating HiRoto® H-nozzle ensures the automatic cleaning of the filter cartridge.
The HiRoto® H-nozzle is the perfect complement for the ePTFE coated HISTec® cartridge filters because it allows a gentle but complete cleaning of the cartridge. In case the filter is dirty, the system starts the cleaning process automatically. According to our experience the filter exchange is needed only after 3 – 5 years!