PlasVent cutting table
Application
- automated cutting of sheet metal
Technical specifications
Width | Length 1,030 mm |
Length 2,060 mm |
1,100 mm | 460 kg | 870 kg |
1,600 mm | 760 kg | 1.260 kg |
1,800 mm | 855 kg | 1,417 kg |
2,100 mm | 920 kg | 1,660 kg |
2,600 mm | 1,200 kg | 2,050 kg |
3,100 mm | 1,300 kg | 2,150 kg |
3,200 mm | 1,400 kg | 2,200 kg |
All widths and lengths are equipped with mechanical/electrical folding control.
The modular design of the cutting table fulfills almost all sizes requirements for cutting tables.
We’ll solve your special cutting needs with pleasure and competence.
PlasVent is a perfected system: flame cutting table & extraction in one
Besides the cutting machine in their entirety and the used material, the cutting table is responsible in major case for the quality of the cutted parts. It must therefore be worked sufficiently precise to achieve the desired quality. Moreover, the cutting table has to ensure effective and efficient removal of contaminated air.
Only in combination with a harmonized on the table and machine filter system and a suitable fan the desired effect, the effective protection of employees and machines, can be achieved. You receive from HERR Industry System a complete system consisting of table, filter system, fan and piping. Additional demands on a good cutting table are derived from ease of installation, further care and maintenance and also energy consumption.
PlasVent cutting tables from HERR Industry System are manufactured from high quality components and meet these demands. The tables are modular and can be adapted to local conditions. The modular design also allows easy transport and time-saving installation. The PlasVent cutting table needs low maintenance. Compressed air lines inside are made of copper and the longevity of the other materials used, effectively reduce follow-up costs in the form of repairs and spare parts.
The optimised exhaust duct, the design of the flaps and the massive construction reduce the need for compressed air and save energy.
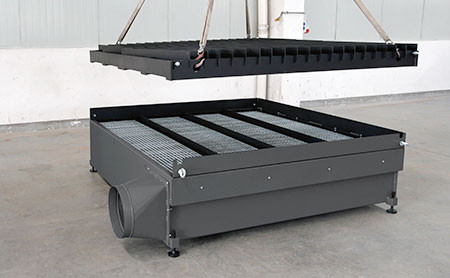
Easy cleaning and maintenance
For exchange of cutting slats, the cutting support can be lifted as a whole using the designated eyelets.
Due to this sophisticated design, the slats can be exchanged in comfortable and timesaving way.
The ease of cleaning and maintenance are further advantages of PlasVent cutting tables.
Simple and quick installation
The tables have lifting eyes and can thus be easily and safely lifted into place.
By 100 mm height-adjustable feet the leveling of the table is simplified and saves installation time.
The compressed air connection of the table modules can be achieved cleanly and quickly thanks to quick connectors.
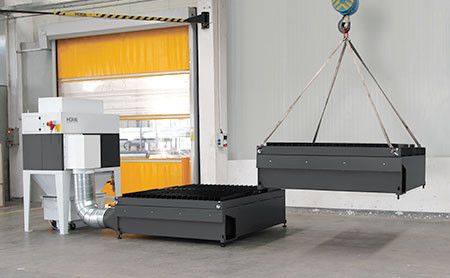
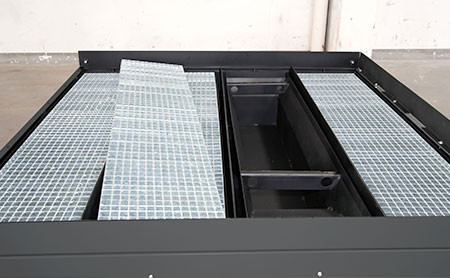
Small parts grid
Optionally available is a small parts grid. The grid prevents small work pieces from falling into the slag boxes preventing a time consuming recovery. Due to its solid design the grid is suitable for plasma and oxy-fuel cutting.
For a table module of a length of 1,030 mm two pieces, for a table module of a length of 2,060 mm four pieces are needed.
Cutting grids
For a perfect cutting result, the choice of a suitable cutting support and slats is indispensable.
HERR Industry System PlasVent cutting tables are equipped as standard with a cutting support including 5 mm thick slats. This support is suitable for continuous plasma and oxyfuel cutting applications up to 150 mm.
For cutting of thin sheets up to 30 mm with plasma, a cutting support with 1.5 mm thick slats is available.
When cutting thick plates (≥ 150 mm) we recommend cutting support with stronger slats or cast iron tips. For such applications, HERR Industry System has cutting supports with 8 mm or 10 mm thick slats in the delivery range. Cutting supports with cast iron tips are available upon request.
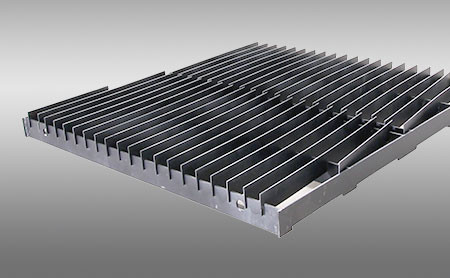
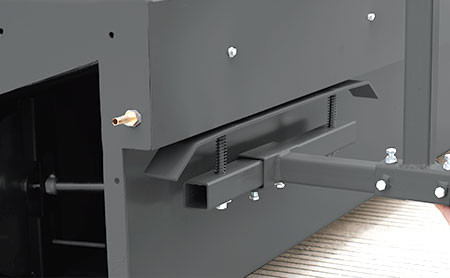
Opening of the exhaust flaps
The opening of the exhaust flaps can be carried out either mechanically, controlled by a mounted on the cutting machine sledge or by CNC. For the mechanical version, the sledge can be easily adjusted to fit to the cutting machine.
If opening of the exhaust flaps is controlled by CNC, the necessary cables for connection to the control box are included in the scope of supply. The advantages of the CNC controlled exhaust flap opening are the reduction of wear parts and maintenance costs.